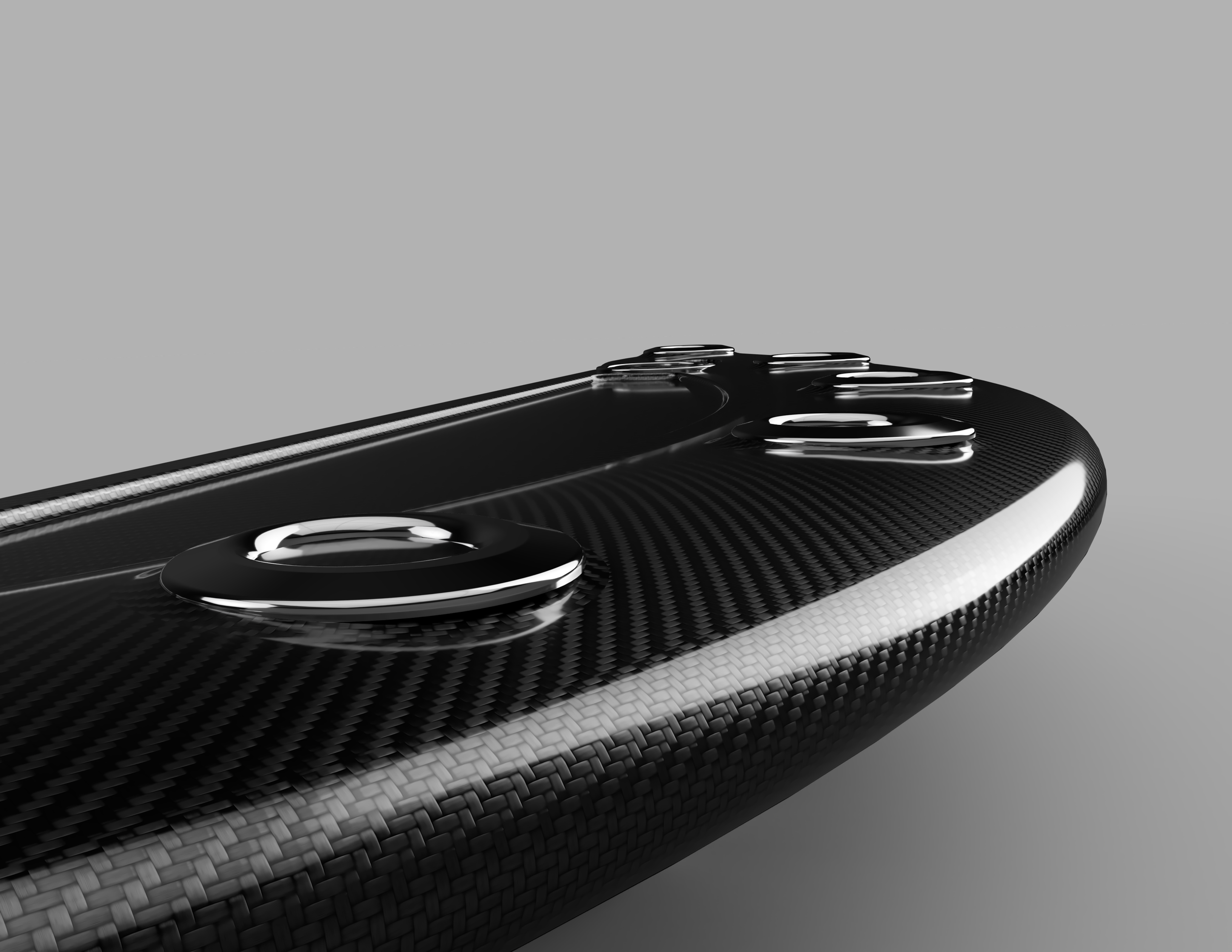
Design
Concept Development
From napkin sketch to production-ready geometry—we refine ideas into manufacturable solutions.
Material Selection
We help identify the ideal composite system (carbon, fiberglass, aramid, thermoplastics) based on your performance, cost, and durability needs.
CAD & 3D Modeling
Precision 3D modeling in SolidWorks and Fusion 360, optimized for composite layups and moldability.
Structural Analysis
Basic FEA to advanced laminate theory and load path optimization to ensure performance with minimal weight.
Design for Manufacturability (DFM)
Design rules that reduce cycle times, defects, and rework in production.
Visual & Surface Aesthetic Design
Designs that perform and look sharp—custom finishes, surface textures, and woven ply symmetry.
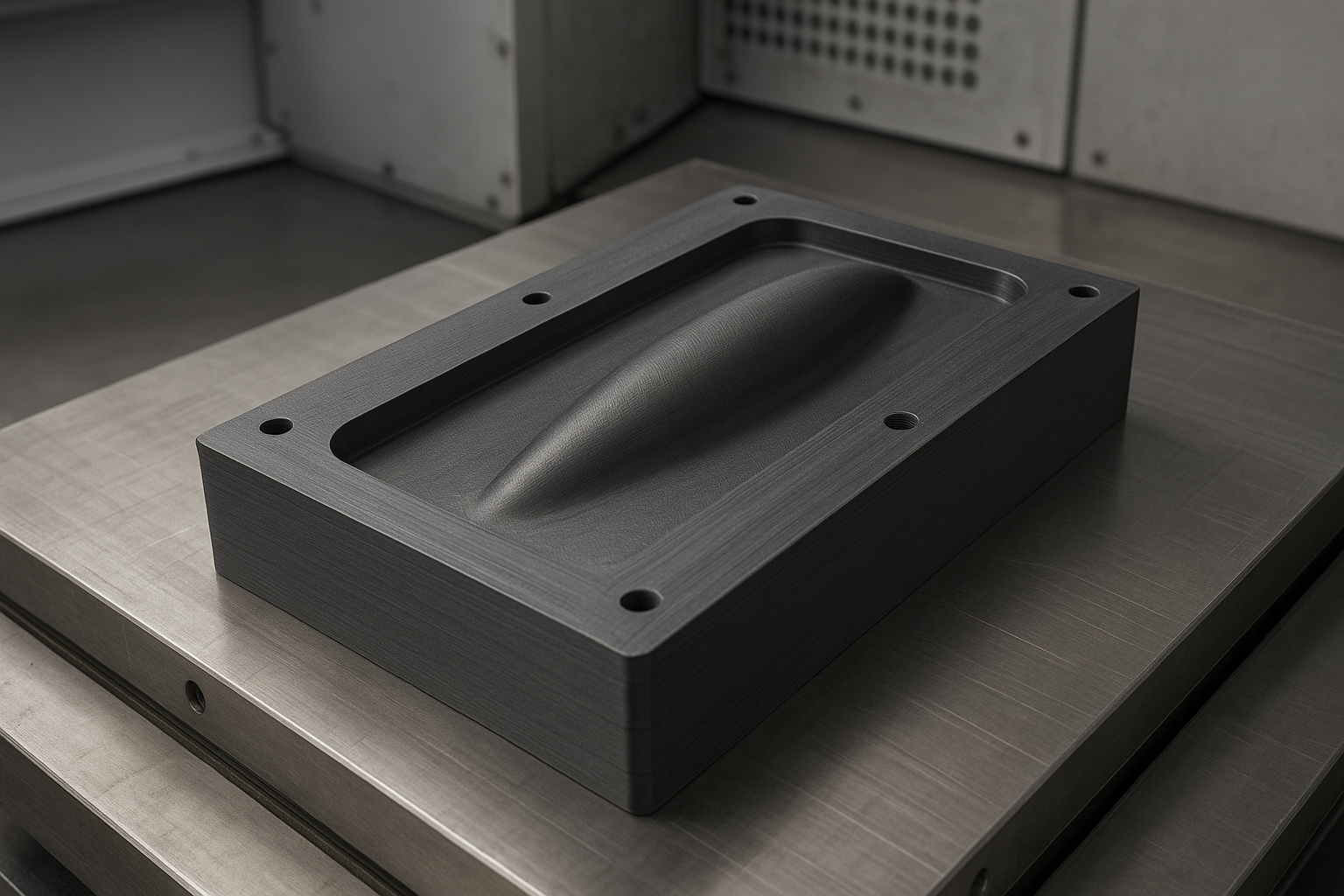
Manufacturing
Mold Design & Fabrication
In-house tooling via CNC and high-temp 3D printing. Supports RTM, compression, vacuum bagging, etc.
Rapid Prototyping
Fast-turnaround parts using printed, machined, or open mold methods.
Composite Layup & Curing
Wet layup, prepreg, vacuum bagging, and custom cure cycles tailored per application.
CNC Trimming & Finishing
Multi-axis precision machining for tight tolerances and clean finishes.
Tolerance Engineering
Repeatable manufacturing to spec for aerospace, medical, and defense-grade parts.
Assembly & Integration
Bonding, insert molding, and multi-material part integration (metal-composite hybrids).